KANSAS CITY, MISSOURI, US — Dominik Bühler, in his World Grain article “Energy Savings Opportunities in Flour Mills,” in 2020, noted that nearly 4% of the total flour cost was for energy, making up 33% of flour processing cost.
Demand in 2022 rose by almost 2% compared with the 2.4% average growth rate seen over the period 2015-19. Global electricity demand is expected to grow at a much faster pace of 3% per year over the 2023-25 period compared with the 2022 growth rate. Undoubtedly, demand for energy is increasing as more grain-based products are being processed to feed the world.
As energy demand increases, so does the costs. Table 1, developed from IAE.org data, shows the high and low First Quarter Cost Index based on the first quarter of 2019 being equal to 100 for Germany, France, the United Kingdom, Spain, the United States, Japan, Australia, the Nordics, India, and European index. The data support two conclusions. The first conclusion is that energy costs are increasing, and the second conclusion is that energy costs vary globally.
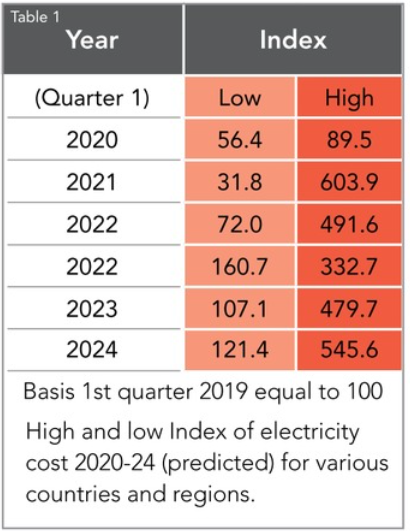
All millers globally do not face the same challenge with respect to energy cost as shown in Figure 1. World Bank data updated in 2021 shows the frequency distribution of the number of countries by energy cost. In some countries the concern is not only the cost but the availability of energy to operate the mill. In some instances, the cost of electrical energy may not apply as some milling locations generate their own electrical power often at significant cost as they purchase fuel to generate energy off the grid, such as facilities on island countries such as Haiti. The capital investment, fuel costs, logistics, operational expenses, and reliability are a significant concern.
Energy costs for countries associated with leading wheat production and/or importation as well as a few importing a significant proportion of wheat consumption are shown in Figure 2. As can be observed, there is a wide range of energy cost among those involved more specifically in wheat milling.
Millers always have been driven to reduce input costs and minimize capital expense. In the past 50 years, there have been numerous articles in milling industry publications and presentations at milling organization meetings focused on reducing energy consumption in milling operations. Reduction in energy consumption is not taken lightly by milling companies, as the margins are small and competition is fierce.
Trades allied with the milling industry including equipment manufacturers, automation and control development companies, energy suppliers and educational institutions have been a significant source of information and technology resulting in reduced energy consumption. The list of technologies and program offerings available to reduce energy consumption and cost has grown tremendously over the years. Financial considerations always have played a role in capital investment whether for productivity improvement or energy reduction and will remain an important consideration into the future. Those facilities with the highest energy cost will have the greatest financial return needed to justify capital expenditures for energy reduction. In some instances, governmental policies and consumer interest may drive investment spending.
The pressure to reduce energy consumption has increased because of consumer interest in environmental issues such as greenhouse gas, ozone depletion, pollution (air, water, land), increasing global temperatures, sustainability, and regenerative agriculture. Like it or not, consumers are demanding accountability throughout their respective consumer supply chain just as companies do, business to business. While consumer motivation and policy changes are significant factors, financial considerations remain at the forefront as millers are in the business to generate profit as well as flour.
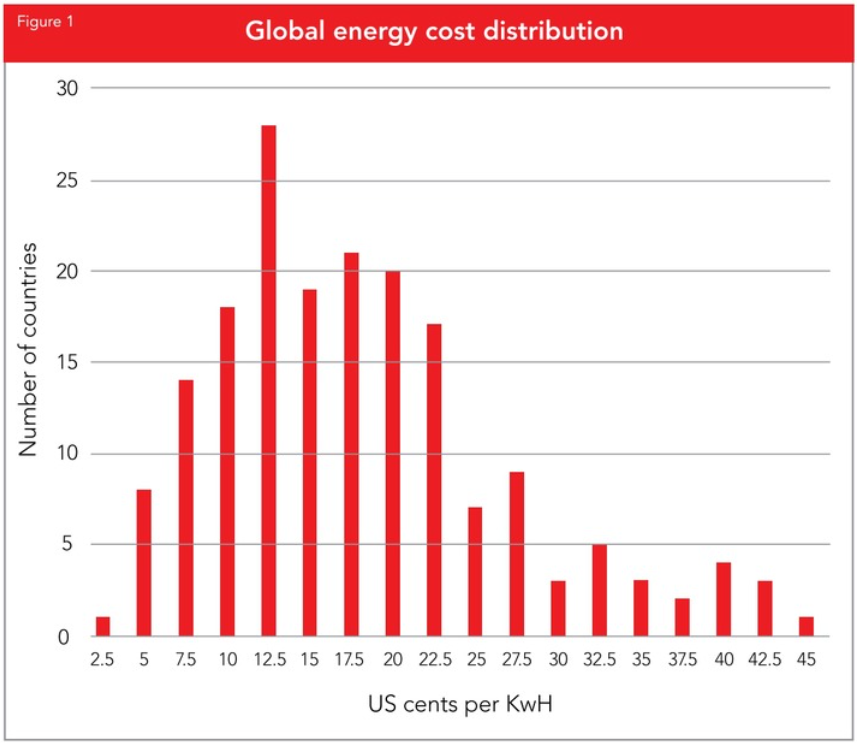
Analyzing the energy bill
Millers must understand what drives energy cost for their facility. This requires examining the energy bill and any negotiated or flexible cost structure between the miller and the energy producer and delivery system. As negotiated and flexible cost on the facility’s electric invoice is more clearly identified and managed to minimize energy expense, so too may capital expense or investment targeting energy cost reduction be properly considered and evaluated.
Agreements and discussion between the energy supplier and the milling company are handled at a higher organizational level than the mill manager or operative. The mill manager and mill operative must have access to the information to assist in identifying the operational issues including scheduling, start times and energy consumption in various portions of the transformation process. Understanding the utility charges and various fees is an important first step.
The source of energy or power varies and may include solar, wind, gas other fuels, coal, nuclear and hydro power. Electricity companies may pull from various facilities with different sources of power that is transmitted across the grid. Electrical power is provided through the distribution system or grid cover the mill’s base and peak demand requirements.
Electrical usage or consumption is the total amount of electricity used in the facility measured in the United States as kWh and is billed at a rate determined by contract. The word “contract” suggests an opportunity for negotiation that can be entered into and may be impacted by electrical energy source flexibility. Electrical demand charges measure the rate of electrical consumption over a period.
Lowering electrical demand
ThCredit: ©SOSLAND PUBLISHING CO.e electrical demand of your plant requires the electric company to build and maintain necessary infrastructure to meet the plant’s energy demand. The demand charge may appear on the invoice or bill as demand charge, demand cost, transmissions and delivery or some other term that should be made clear to the miller.
The demand for electricity in your mill may vary over the course of the day and it is the peak demand during the month upon which the demand charge is billed. Electric motors when turned on experience a significant current in rush to overcome inertia and cause the motor to turn. That inrush of energy (amperage) is 7 to 9 times greater than the full load amperage rating of the motor. Starting a motor is certainly a peak demand period for that motor. Now imagine how much demand would be required to start all the motors in the mill at once.
There are various types of demand charges depending on contract language. Actual demand is the observed peak from last month. Billed demand may be an adjustment to real demand based on when the demand occurs, for example, “coincidental peak clauses,” facility peak demand when the grid is at its peak or “ratchet clauses,” 80% of maximum demand from the last 12 months.
Lowering demand costs requires managing your mill’s load profile using one of two main strategies. The first strategy is load-shedding where certain units of the facility may be shut down temporarily to reduce demand. The second strategy is to transfer load to off peak hours. Some utilities offer incentives to shed or shift load during high grid stress events.
Electricity consumption on the grid typically cycles each day with the lowest demand occurring around 5 a.m. and the highest demand occurring at some point during the day (depending on the season), before falling back down during late evening hours. This variation in electricity demand follows the daily patterns of energy use by households and businesses, but it is especially dependent on weather-related factors.
Hourly electricity load in the United States is generally highest in the summer months when demand peaks in the afternoon as households and businesses are using air conditioning on hot days. During the winter months, hourly electricity load is less variable but peaks in both the morning and the evening. Load is generally lowest in the spring and autumn when homes and businesses have less need for space heating or cooling.
Clearly, there are many factors contributing to energy costs in a milling operation hidden in the electrical bill itself. There are contractual discussions to be had with the mill’s electrical suppliers as well as internal operational management decisions that can be made to reduce demand and peak demand charges or costs.
In addition to basic consumption and demand charges, there are often fixed charges associated with simply being a customer and having a meter that must be monitored and maintained. Also, there are various taxes, fees and penalties that may be incurred. The penalties may include late payment fees as well as power factor penalties to be presented in the next article.
Jeff Gwirtz, a milling industry consultant, is president of JAG Services, Inc. He may be reached at [email protected].