KANSAS CITY, MISSOURI, US — Ship loading and unloading equipment suppliers are working to balance more stringent environmental standards, including less noise and dust emissions, with customers’ demands for improved energy efficiency and higher handling capacities.
“When our customers call on us, they are obviously looking for low energy consumption and high performance, even in extreme conditions, as well as a robust and reliable machine,” said Vigan Engineering, one of the suppliers who responded to World Grain’s annual survey.
In the last 10 years, those demands have evolved toward a reduction in dust emissions. With more and more homes being built closer to industrial areas, customers are looking for ways to reduce the nuisance.
The grapple is a simple tool that has been used for a long time, but it generates a lot of dust, Vigan said. The company uses pneumatic suction technology, which has the advantage of generating very little dust.
“Our systems incorporate overpressure filters that keep the dust inside a closed circuit,” the company said. “Our machines are fitted with a telescopic tube that can be extended by 50% and are installed on a ferrule to ensure effective suction of the entire boat. The turbines, electronics and compressors for filter regeneration are located in the cabin. Our systems enable emissions of around 3 milligrams per cubic meter to be achieved or not exceeded.”
Grain handlers with port locations in urban areas also are concerned about the noise level generated by ship loaders and unloaders. Machines can have a monotonous noise but can also generate sound changes, for example when a valve or piston is activated, Vigan said.
“We have to carry out in-house acoustic calculations and target the sources of noise in order to achieve an acceptable level,” Vigan said. “Generally, we are asked not to exceed 60 to 65 decibels.”
Achieving this sometimes requires specific insulation measures for the components. The transfer of grain, when it comes into contact with tubes, elbows or bars, will emit noise. These can be acoustically insulated using an aluminum wall a few centimeters thick, Vigan said.
“We can also provide a silent exhaust at the top of the cabin, where the air will be directed toward the least sensitive areas, as well as acoustic panels between the outer metal wall of the cabin and the interior volume,” Vigan said. “Finally, the turbine can be cast in a concrete matrix to reduce noise emissions.”
Overall, suppliers say business is holding steady or experiencing some growth, but political issues are delaying some projects. Commodity price volatility and price increases for steel and electrical components are also making business difficult.
In addition, the war in Ukraine that started in February 2022 continues to impact equipment suppliers. As a leading grain exporter, Ukraine was one of the most active regions for ship loading and unloading equipment prior to Russia’s invasion.
Melle, Germany-based supplier Neuero said it is fortunate to have partners who understand the situation. Steel structure suppliers have suffered twice, first in rising costs and then sudden project stops.
“We are doing our part and helping to pass this difficult situation,” Neuero said. “We know that it is easy to make money in the short term but better is a long-term strategy to be steady in the future.”
Ukraine is an important market, particularly for ship loaders, said Bedeschi, a ship loading/unloading supplier based in Limena, Italy.
“The major challenge so far is supporting existing equipment regardless of the political situation,” Bedeschi said. “Remote support has been crucial in this period.”
With export structures and silos being destroyed, there were many requests for temporary and flexible solutions to maintain continuity in providing grain to the world, Vigan said.
“Vigan has been doing the utmost to answer these demands,” the company said. “It will, however, remain a challenge to maintain export figures at the required pace.”
Currently, some of the most active areas in the world for ship loading/unloading capacity expansion include North America, South America, Africa and Australia.
“Replacing equipment with more advanced ship loaders/unloaders is becoming more interesting compared to maintaining or updating older technology facilities,” Bedeschi said. “Our philosophy is to provide a dedicated solution rather than a standardized and less flexible machine.”
Looking ahead, remote data collection and assistance are becoming more essential in offering customers maximum efficiency, the company said. It can help prevent breakdowns by optimizing maintenance and allow for intervention in the event of a malfunction.
Bedeschi is working with its research and development department to implement remote assistance through VR. Multiple people could connect in the same virtual scene to provide technical assistance or explain certain specifications or features.
Quiet unloading in Germany
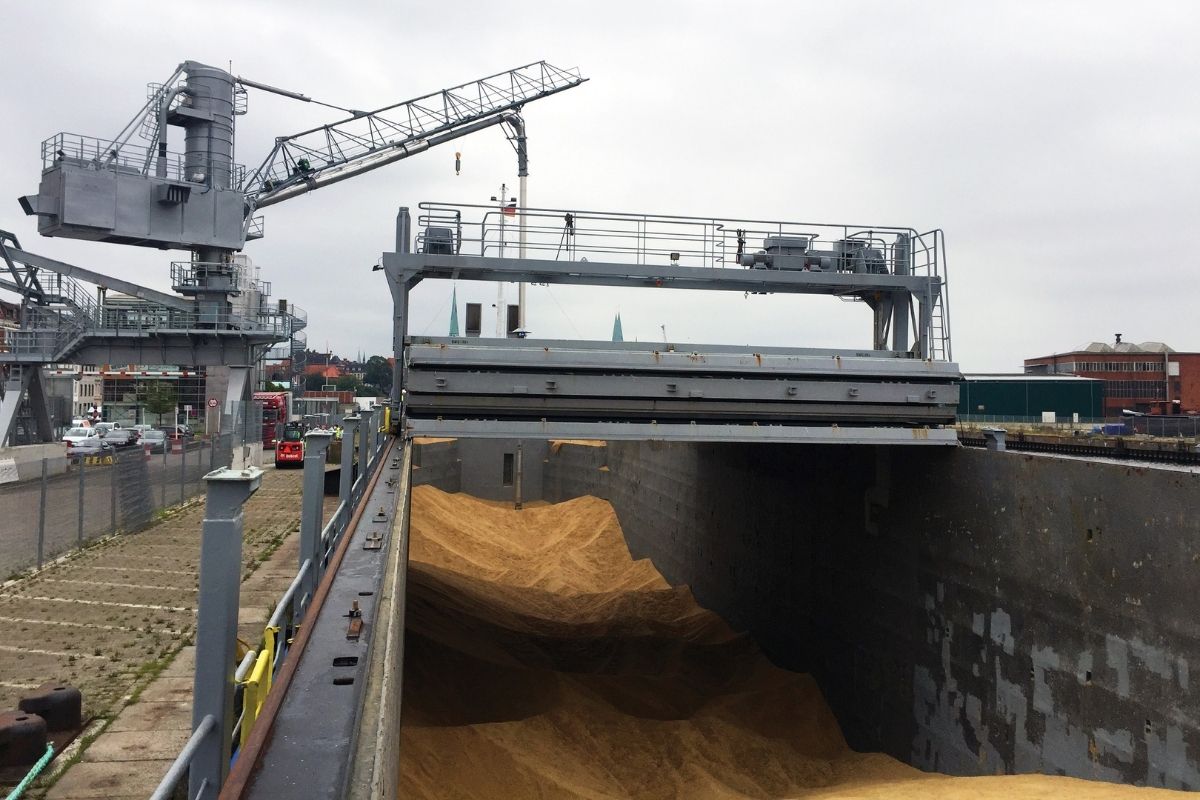
Vigan provided several noise reduction solutions for Brüggen’s ship unloader in Lübeck, Germany.
| Credit: ©VIGANCereal-based foodstuffs producer Brüggen invested €30 million ($32 million) in updating its Lübeck, Germany, facility including a new ship unloader, a new silo for raw oats, an oat cleaning and hulling line and an additional building to produce muesli. The family-owned company produces a wide variety of raw materials as well as finished goods such as corn flakes, wheat flakes, muesli, puffed cereals, granola and more.
Vigan, based in Nivelles, Belgium, supplied a NIV ship unloader that has a capacity of 120 tph and is equipped with several noise reduction solutions.
These solutions include an insulated elbow and under-elbow flexible components with noise cover that are specifically designed to capture and disperse noise generated by the machinery. This significantly curtails the noise emitted into the surroundings.
Insulated horizontal oversized exhaust silencers diminish noise produced by the expulsion of exhaust gases from the machinery. The machine room is equipped with insulation featuring perforated plates to prevent noise leakage while the turbines are engineered for quieter operation.
Inlet and outlet air silencers are integrated into Vigan ship unloaders to decrease noise levels at the points where air is drawn in and expelled.
Horizontal pipe, elbow and vertical fixed parts of piping are acoustically insulated with additional enhancements such as a cap, relocated air inlet adjusting device and a rubber coating to further mitigate noise.
Lastly, roof insulation aids in achieving the desired noise reduction goals.
“The implementation of noise protection systems in agri-bulk ship unloaders is a crucial aspect of their design and operation,” Vigan said. “These systems serve to minimize the impact of noise on the surrounding environment and safeguard the well-being of both workers and nearby residents.”
Terminal moves ahead in Ukraine
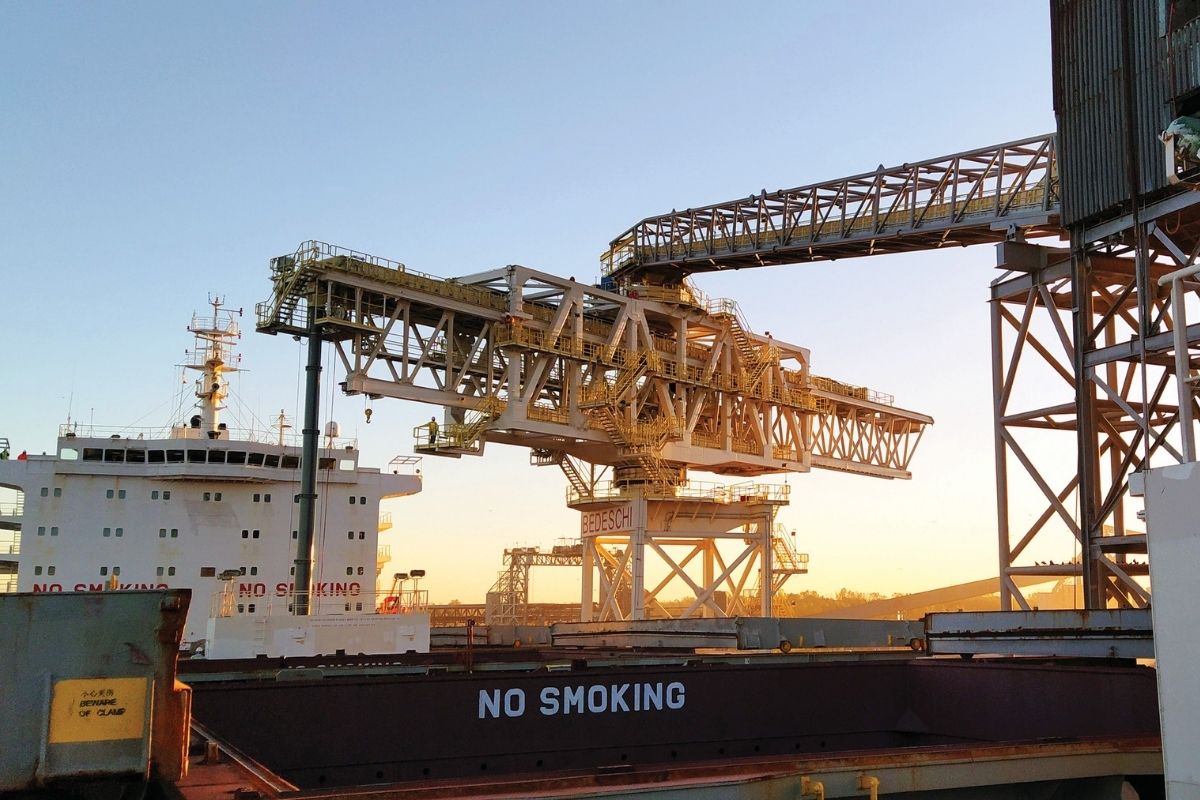
Equipment supplied by Bedeschi at the Cargill Westwego terminal in New Orleans, Louisiana, US, is in place and successfully operating.
| Credit: ©BEDESCHIRisoil was in the process of constructing a bilateral pier in the port of Chornomorsk in Ukraine, capable of handling loads on each side of the structure, when Russia invaded in February 2022.
Neuero was just loading the first trucks with the loading/unloading equipment, which was 95% complete, when the invasion happened. Risoil stopped the project, and given the situation, Neuero said it postponed sending invoices.
“We evacuated our supervisor who was already at the installation site via Moldova and Romania because all major cities were attacked,” Neuero said.
Six months later, Neuero received the green light to continue the project, even under the war circumstances.
“Remote assistance and local experienced people made it possible to start this terminal,” Neuero said.
The facility includes two loading lines, each with a capacity of 1,500 tph, and an unloading line with a capacity of 600 tph. With six loading arms, ships can be loaded on one side, or two ships can be loaded at the same time with one on each side. In the middle is the pneumatic unloading boom. There are three fixed steel towers displaced at 60 meters.
All arms are equipped with kick-in, kick-out movement (KIKO) and dustless loading heads (DLH). Cost for the total project was UAH 1.5 billion ($41 million).
Neuero supplied a 1,000-tph ship loader to Risoil several years ago, so it was aware of Neuero’s reliability and efficiency.
“This challenging new project was perfect to drive in another era of Ukrainian grain exports,” Neuero said. “It was an honor to be part of it.”
Chornomorsk is one of the largest terminals in the country for the transshipment of vegetable oil and grain. It was designed and built in stages. Since 2020, it has expanded to include transshipment of bulk cargoes and packaged goods.
“We strongly believe that despite the difficulties we face, in particular the tense situation with exports in the Ukrainian ports on the Black Sea, such projects become even more important for the development of the industry, maintaining and increasing jobs, and therefore, additional income to the budgets,” said Risoil founders Oleksandr Minov and Shota Khadjishivili.
Louisiana port sees success
Cargill Westwego recently completed a refurbishment and upgrade of its grain export terminal in New Orleans, Louisiana, US.
Bedeschi supplied a 2,200-tph ship loader for the Mississippi River facility. The company engineered, manufactured, installed and commissioned the shuttle type ship-loading arm. It can load grain and oilseeds at 80,000 bph on vessels up to 120,000 dwt. Bedeschi also undertook the mechanical and electrical works on a turnkey basis.
The equipment, which was assembled in Italy and transported to New Orleans, has reached its final position and is successfully operating.
Bedeschi said it prioritizes sustainability in order to reduce the impacts of waste on the environment by developing efficient solutions for reducing emissions, spillages and any kind of pollution.
“Thanks to our Bedeschi Service, we monitor all phases of the project in order to optimize costs, time and maintain good productivity,” Bedeschi said.