KANSAS CITY, MISSOURI, US — Food security is top of mind for grain storage and handling companies across the world, as political instability and trade restrictions cause global supply chain disruptions and shortages.
For equipment manufacturers and suppliers, that means demand is increasing for greenfield facilities, said those who responded to a survey by World Grain.
“Demand shocks and grain price volatility over the past two years have put state investors under pressure to construct new grain storage and milling facilities as strategic investments to free the country from short-term import dependency and ensure medium-to long-term food security and stable market prices,” said CESCO EPC.
Importing countries are looking to ensure self-sufficiency, either by installing internal grain terminals to sustain local production, or by opening new port terminals for strategic storage of imported grain, it said.
“Both government and non-government organizations are seeking to secure food safety by creating new facilities for cereals,” said Sedat Demirbas, international sales executive of Altinbilek. “We are receiving high demand from different continents and demand is increasing day-by-day while the war in Ukraine continues.”
With grain prices increasing due to the lack of supply from Ukraine and Russia since Russia’s invasion in February 2022, countries such as Saudi Arabia are looking at longer-term grain storage periods for security purposes, one supplier said.
Geographically, demand is strong in Mexico, Central America, the United States, North Africa, Southeast Asia and eastern Europe. Projects and contracts in Russia came to a standstill following its invasion of Ukraine.
Preserving grain quality and minimizing losses during storage is an ongoing concern. Customers are looking for storage protected from atmospheric influences. They want advanced solutions for grain monitoring and conditioning systems using temperature/humidity sensors, ventilation, cooling and fumigation strategies. Corrosion resistant steel is also in demand to deal with increasingly volatile climate conditions.
Larger storage capacity and corresponding conveying/processing capacity are in demand, CESCO said. The company has supplied a silo storage facility with a capacity of 300,000 tonnes and is active in tenders for ever-larger capacities.
Supply chain issues that started during the COVID-19 pandemic have eased, but there are still some ongoing concerns that have required creative solutions.
“At the end of the pandemic, the shortage of electrical components for control systems also resulted in longer delivery dates, which required finding special solutions together with our customer to reduce the impact on the schedule and ensure the timely completion of projects,” CESCO said.
Sweet Manufacturing Co. has had multiple issues with vendor and component delays. The company has tried to rethink its inventory levels and increase machine and labor hours.
Supply chain issues have caused longer lead times and higher prices. AGI said it has been actively collaborating with its customers to work through any supply chain concerns so projects are not affected.
Demirbas said Altinbilek hasn’t had problems with raw material shortages, but fluctuations in market prices and high inflation are concerns.
“Prices from suppliers are changing on a daily basis,” he said. “This is an obstacle for project sales, which requires time to design, build and deal.”
AgCentral adds third bin
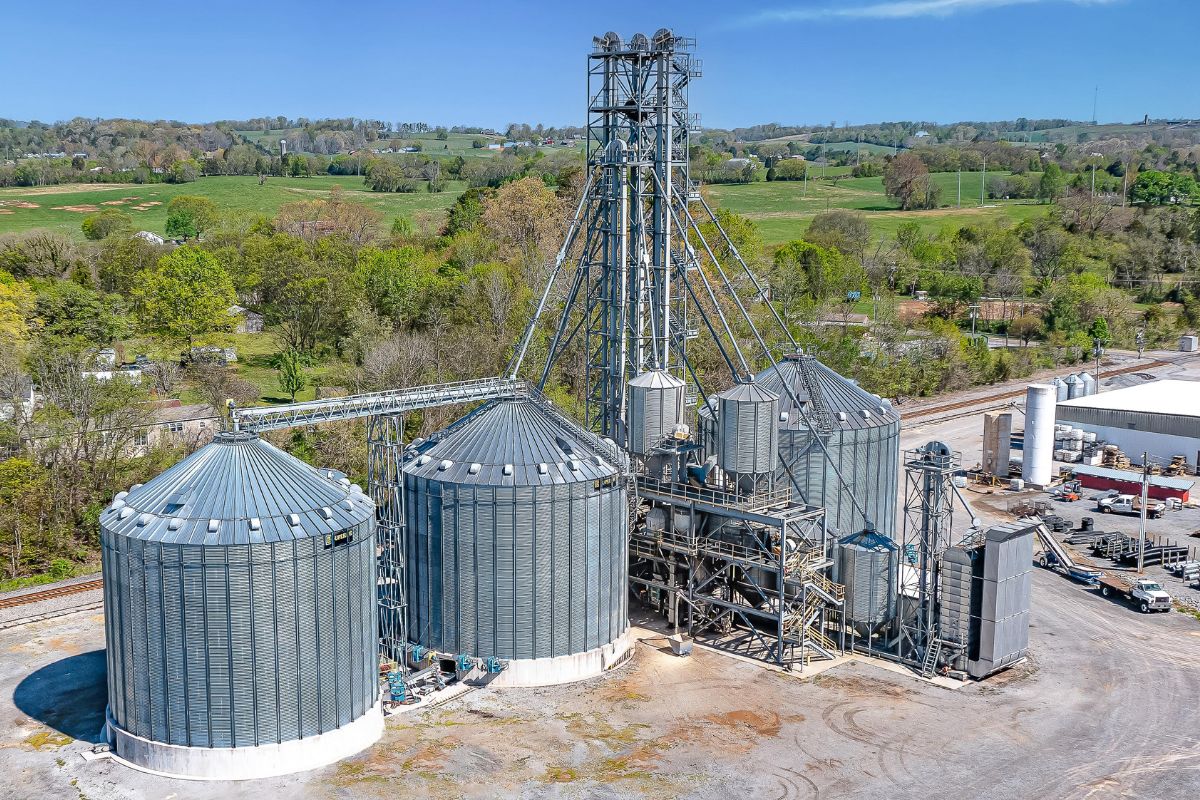
To keep up with customer demand, AgCentral Cooperative added a third commercial bin at its facility in Greenback, Tennessee, US, bringing overall capacity up to 372,300 bushels. The facility, designed and built by Superior Grain Equipment in 2017, now includes three 60’ x 12-ring 117,500-bushel commercial bins, six 3,300-bushel wet hopper tanks and a 1610 model mixed-flow dryer rated at 1,050 bph. The facility handles corn, soybeans and wheat.
AgCentral came to Superior Grain Equipment, based in Kindred, North Dakota, US, with a unique request — they wanted to unload and load grains as well as dry and roast soybeans at the same time, and not have a bottleneck. Feed is a primary product for AgCentral, and it wanted to create a market for current members to buy a locally grown product.
Superior was able to custom build a full-service facility to meet these needs. Superior’s design and engineering team integrated many facets of a grain facility, a storage facility, a drying facility with hammer mill operation, roller mill operation and a roasting operation.
AgCentral offers flexibility beyond what most facilities offer.
“There isn’t anything like this in the Tennessee area,” Super Grain Equipment said. “AgCentral’s facility gives farmers a much more efficient way to market their crops. They can intake soybeans, corn and wheat from local farmers. At the same time, AgCentral can grind and hammermill material that gives members a finished product to load out for feed application.”
Feedco completes grain storage in Saudi Arabia
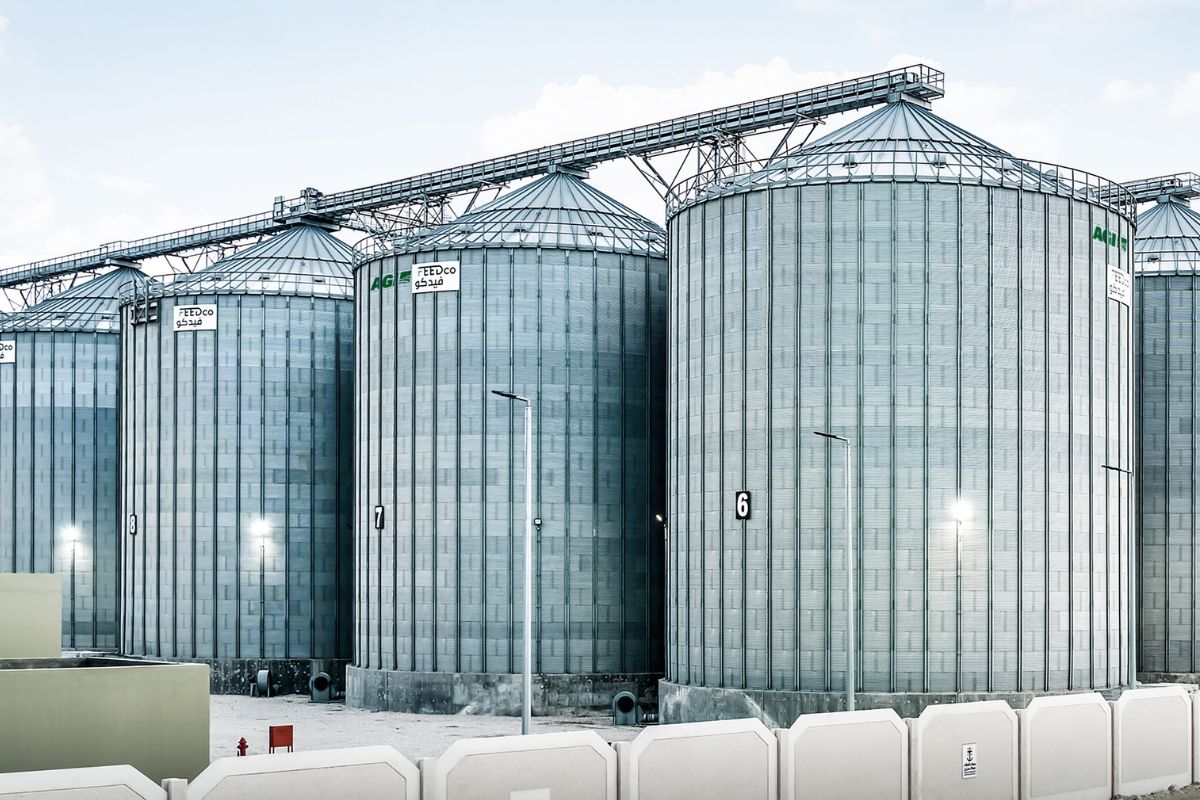
Feedco Investment Co. completed in the fall of 2022 a 77,500-tonne grain storage and handling facility in Dammam, Saudi Arabia, as part of its over-arching initiative to advance animal food security. The facility was designed to handle the demand for grain across Saudi markets and provide flexibility to grain importers.
Immediately after completing the trial and test run in September 2022, the facility received 70,000 tonnes of corn.
Based in Winnipeg, Manitoba, Canada, with worldwide manufacturing and engineering operations, AGI supplied the project with a complete solution including grain silos and accessories, handling systems, packaging equipment as well as pre-cleaning and weighing equipment.
The facility is an example of a turnkey project in which Feedco relied on one supplier. It took four months to install the AGI silos and handling equipment. After installation, an AGI technical supervisor was on site for about two weeks to commission the facility.
The installation features AGI FRAME heavy duty, steel grain storage including 10 flat-bottom silos; three bulk loading silos; and all related accessories, including catwalks, sweep augers, aeration, temperature sensing systems and electrical equipment.
AGI PTM grain handling equipment included chain conveyors with 400 tph of loading capacity and 200 tph of unloading capacity; flight conveyor; and bucket elevator.
Pre-cleaning equipment included a rotary drum pre-cleaner, with a capacity of 300 tph and the weighing line included an inline electronic scale. The packaging/grain filling machine has a capacity of 700 bags per hour.
Feedco provides an integrated feed system for the Saudi Arabia livestock sector and supports the supply chain through storage and handling units with a capacity that can hold up to 1 million tonnes of grain per year. Feedco also works in other sectors, including veterinary drugs and special laboratories.
The Dammam facility was AGI’s first project with Feedco. A second project is currently underway to install a 25,000-tonne silo for feed at Feedco’s new site in Jeddah, Saudi Arabia.
More bins for Ukrainian facility
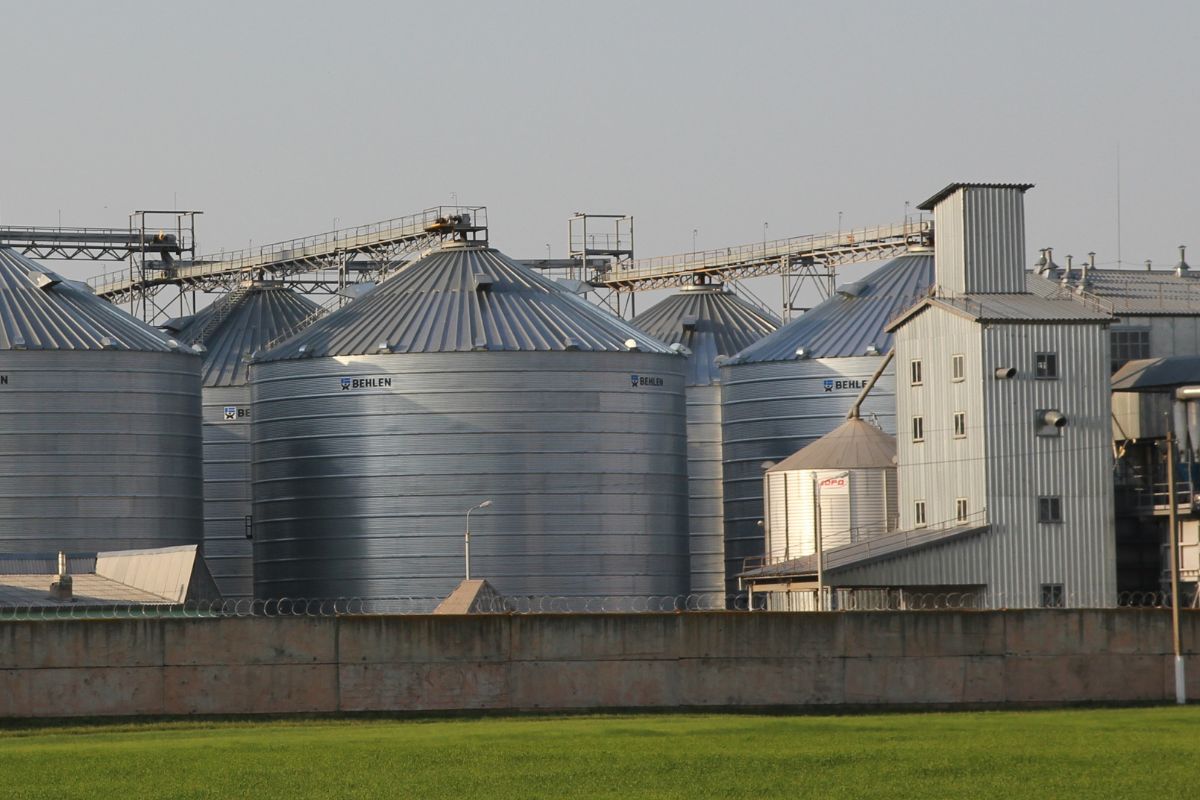
Since 2010, Zemya I Volya LLC in northern Ukraine has been under near constant construction and expansion. The grain storage facility in the Chernihivsky region handles wheat and corn. With the most recent delivery of 10 storage silos, completed in 2020, the site has a total capacity of nearly 370,000 cubic meters.
Zemya I Volya has worked with Behlen Manufacturing Co., based in Columbus, Nebraska, US, and partner The Adept Group, for its storage needs since 2008. During that time, they supplied the company with more than 90 Behlen silos.
At the Chernihivsky facility, Behlen and Adept first supplied 14 inside stiffened grain silos Model 22x16 in 2014 followed by nine bins in 2016, nine bins in 2017, 12 bins in 2018 and 10 bins in 2020, for a total of 54 Behlen silos.
Each individual silo is 22 meters in diameter and 16 meters to the eaves with peak heights of 22 meters and a capacity of 6,846 tonnes.
Zemya I Volya has 32,500 hectares of agriculture land and produces mainly corn. Given the significant seasonal fluctuations in the cost of corn, having its own storage allows Zemya I Volya to sell grain at the best price.
Because the last batch of silos was shipped during the COVID-19 pandemic, there were several hurdles in getting the product moving and on site. When COVID restrictions were being implemented, four shipments were spread out from Behlen’s factory in the United States to the port in Odessa, Ukraine.
“This took a lot of coordination on the part of Behlen, Adept, freight forwarders and the client to get all of the containers delivered to the client’s site in northern Ukraine,” Behlen said. “As this is a rural site in Ukraine, there were not a lot of extra complications to construct the last shipment of silos once they arrived.”
Austrian grain company merges facilities
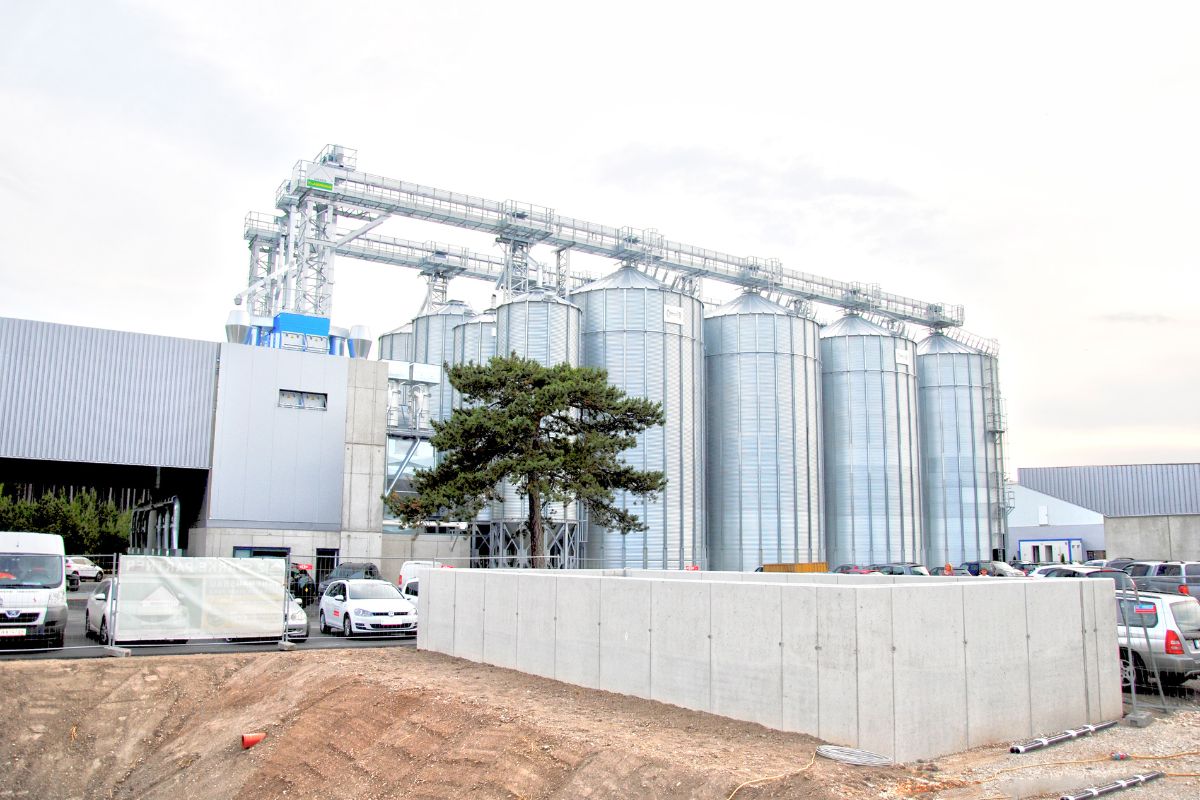
Raiffeisen Lagerhaus (RLG) merged two sites in southeast Austria to create a new greenfield installation in the heart of the catchment area. The existing facilities were old and RLG, a major player in the Austrian grain industry, wanted to improve its economic efficiency.
For the new facility, RLG turned to Cimbria, based in Thisted, Denmark, for its handling equipment. The first section of the new plant includes two parallel reception lines, each with an intake pit and pre-cleaning unit. One Delta 146 and one conical wind-sifter were installed inside the pre-cleaning tower.
The product is transported to the silos by Cimbria chain conveyors and bucket elevators at a capacity of 100 tph, corresponding to a reception capacity of four trucks per line, per hour. Automatic foot cleaning systems at the elevator boot help keep the plant clean and prevent cross-contamination of crops.
Within the silo section, with a total holding capacity of 7,750 tonnes, there are four blocks with the following configurations:
- Two hopper silos with a holding capacity of 125 tonnes each, mainly used as wet cells prior to drying or as load-out bins for the bulk loading unit.
- Six hopper silos, 250 tonnes each, for storage of smaller batches or as load-out bins.
- Four hopper silos, 500 tonnes each.
- Four flat-bottom silos, 1,000 tonnes each.
The drying section includes a continuous dryer for indirect heating with oil, as well as a box dryer for smaller quantities of niche products.
In providing solutions for the facility, Cimbria considered the area’s relatively high earthquake zone and strict noise levels for emissions.
AlSahl invests in three Libyan grain facilities
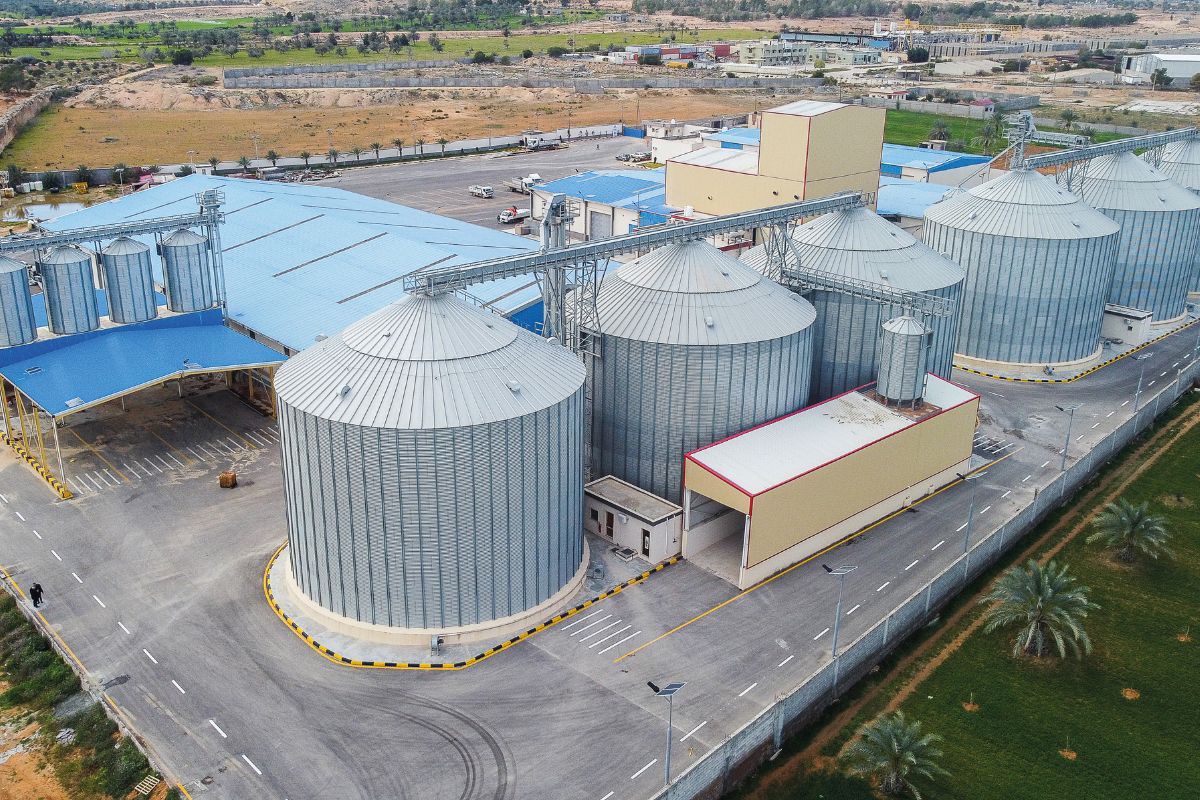
As part of its investment in modernizing the food industry in Libya, AlSahl Group recently completed three grain storage facilities for processing and trading of wheat, barley and rice. Located in Tobrouk, Tripoli and Bengasi provinces, the facilities have a total capacity of 119,500 tonnes.
The facilities were built in different regions of the country to take advantage of local characteristics and the economic network. Each plant has a different approach and scope and has been adapted to different requirements.
AlSahl worked with CESCO EPC, based in Konstanz, Germany, and Simeza, based in Utebo, Spain, on the storage silos and handling equipment for the facilities.
Simeza supplied the following silos in each phase of the project:
Phase 1: Five silos, 5.090 tonnes each; two silos, 60 tonnes each; and four silos, 100 tonnes each.
Phase 2: Six silos, 5.090 tonnes each; two silos 60 tonnes each; and four silos, 100 tonnes each.
Phase 3: 12 silos, 5.090 tonnes each; three silos 60 tonnes each; and 12 silos 100 tonnes each.
Simeza also supplied catwalks, lateral supports and towers; vertical ladders; temperature systems; ventilation systems; level indicators and sweep augers.
CESCO supplied the handling and conveying equipment, including 15 CC400 chain conveyors with a capacity of 200 tph; 12 CC350 chain conveyors with a capacity of 150 tph; and three BBE370 bucket elevators with a capacity of 200 tph.
It also supplied two intake pits: 12x4 square meters with a maximum load of 12 tonnes and 3x4 square meters with a maximum load of 12 tonnes. The intake dust aspiration system included six fans with a capacity of 66 cubic meters per hour.
CESCO also supplied control panels, flow pipes, a loading bellow with a capacity of 250 cubic meters per hour, a pipe magnet for manual cleaning with a capacity of 260 cubic meters per hour, complete engineering of the plant, supervision of erection and startup and a set of spare parts.
The new facilities will help AlSahl with distribution of cereals and storage for further processing for production of pasta, couscous and flour.
AlSahl has a significant presence across the food value chain in Libya, from production to distribution and retail. It is focused on improving domestic food production, processing and distribution, and contributes to food security by producing and distributing finished food products and agribusiness products.
It produces and/or distributes pasta, couscous and flour; vegetable oil; dates; cakes, cookies and croissants; and poultry meat. Its activities related to agriculture include import of corn, wheat and barley; import and distribution of cereals in Libya; and agricultural investment and distribution of fertilizers and seeds.
Agrosilos adds to rice storage facility
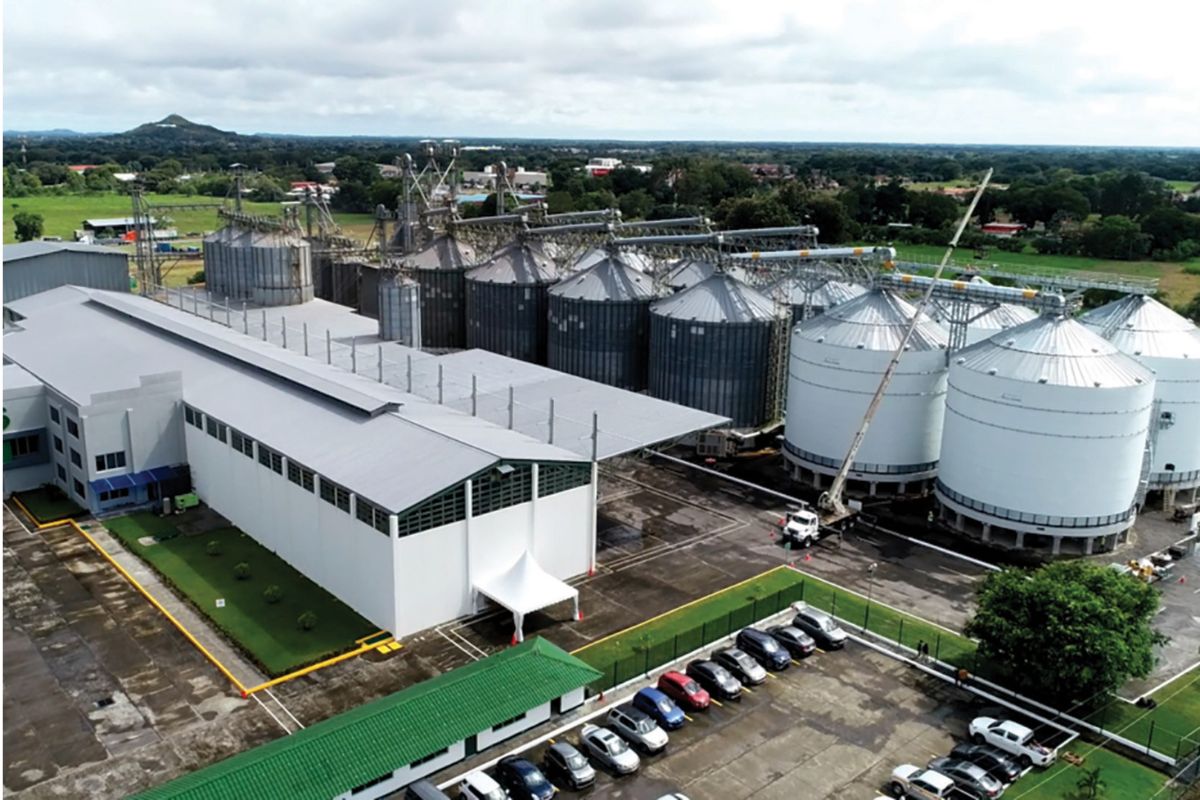
Agrosilos, SA completed an expansion project at its rice storage plant in David, Chiriquí, Panama last fall. The expansion included the addition of four new silos with a capacity of 5,500 tonnes each, bringing total capacity at the facility to 66,000 tonnes.
The facility is one of the largest paddy storage sites in central Panama. Since starting operations in Panama in 2010, Agrosilos has grown along with the rice sector. The company specializes in receiving, storing, processing and distributing the leading rice brand in the market, Arrossisimo.
Because of the highly humid environment and exposure to ocean spray water, the equipment and steel quality must be able to withstand a highly corrosive environment.
Sweet Manufacturing Co., based in Springfield, Ohio, US, supplied four 36-foot flange channel covered belt conveyors to load and unload the silos, using G140 steel. All the conveyors included 4B monitoring sensors for misalignment, bearing temperature and emergency stop and plug conditions. Sweet also supplied the handling equipment in 2010 for the first set of silos.
New corn facility to supply Venezuelan Arepa mill
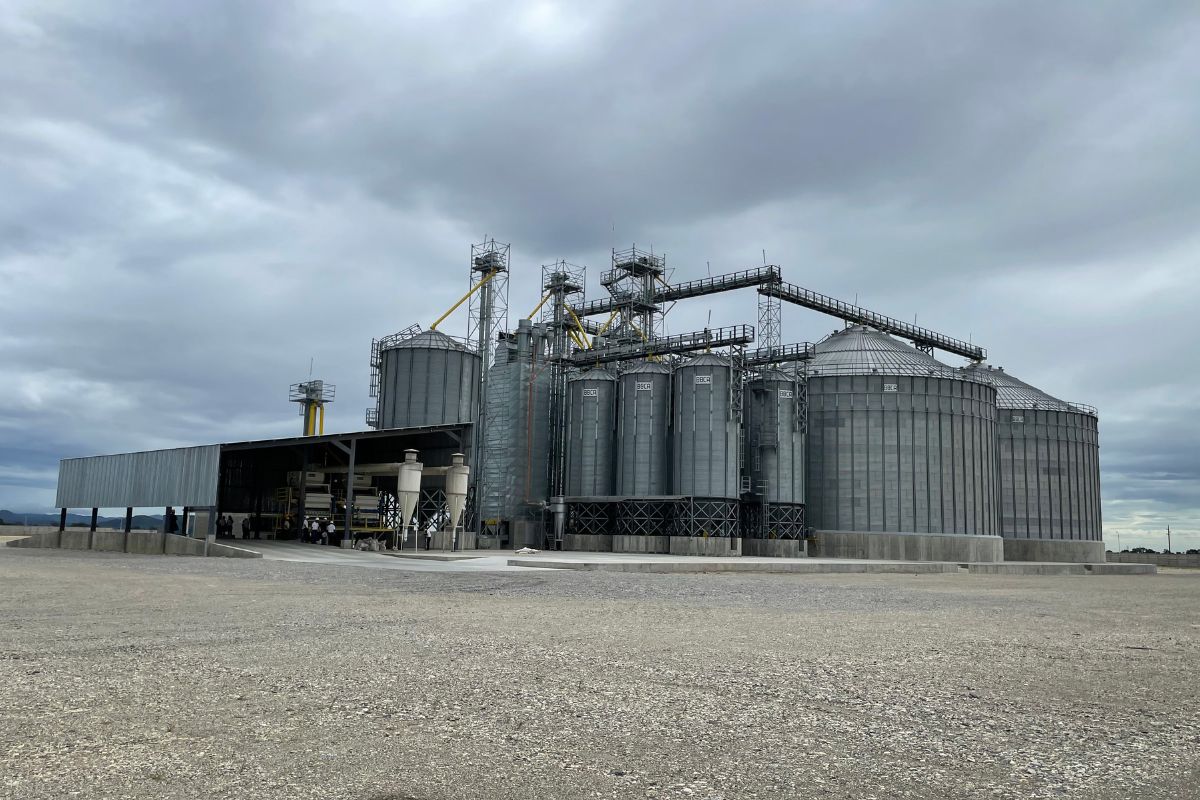
Inproa Santoni CA completed a storage plant in Araure, Portuguesa, Venezuela, that will provide corn for a new Arepa flour mill, providing food security for the region. Arepa is a traditional type of bread made with corn flour and is a critical food for the region.
The project is part of a national food supply program in Venezuela, as high inflation and an unstable supply chain are impacting global food prices.
It took 12 months to complete the project, which includes 31,500 tonnes of storage. Altinbilek Group, based in Eskisehir, Turkey, supplied the entire project, its first in Venezuela. Along with design and engineering services, it supplied two 27.38-meter flat-bottom silos with an overall height of 22.79 meters and an eaves height of 15.17 meters and several hopper silos including: one bin with an 8.21-meter diameter, six bins with a 5.48-meter diameter and one bin with a 4.56-meter diameter.
All of the steel was S350 Magnelis steel and the bolts were JS1000 coated grade 8 (10,9) fasteners. The plant is equipped with two dryers and conveying capacity is 100 tph.
This was Altinbilek’s first time working with the Santoni family.
More than 20 hopper silos for new Spanish flour mill
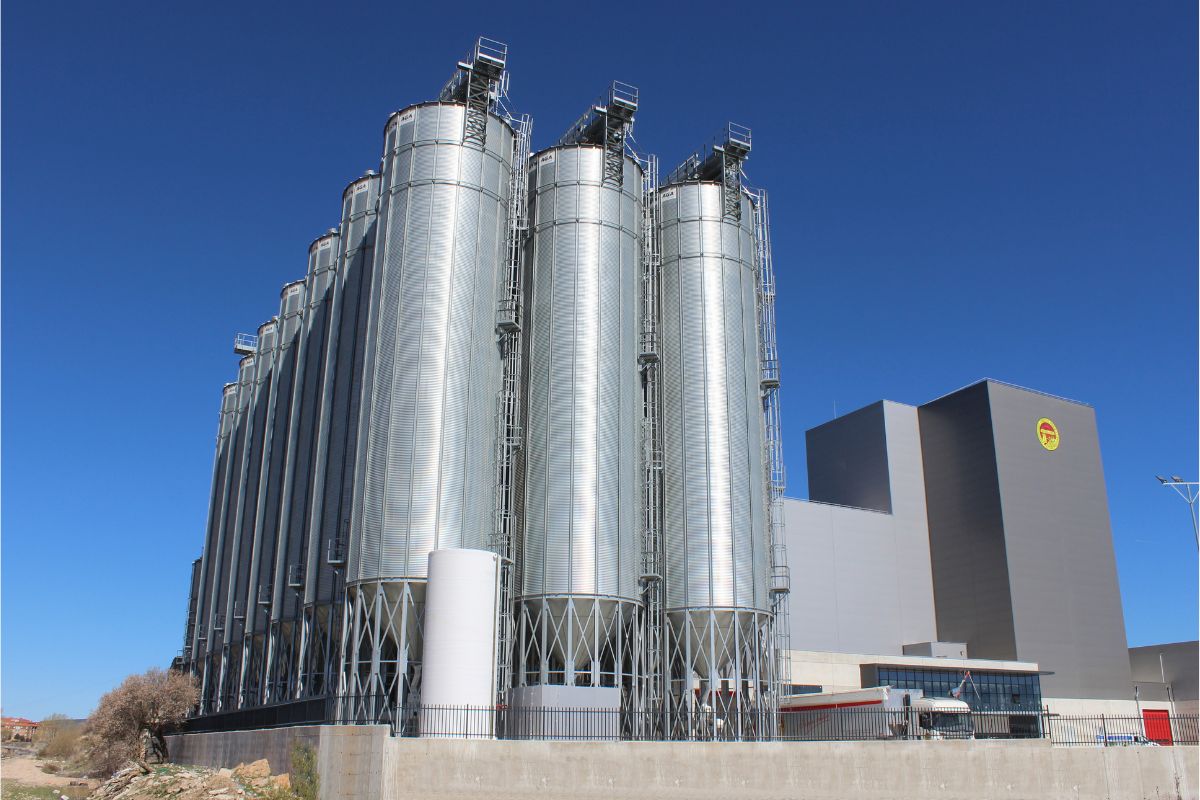
Panificadora Conquense Agrícola recently completed a state-of-the-art flour mill in Cuenca, Spain, replacing its existing mill in the city center and almost doubling production and storage capacity.
As one of the largest flour mills in Spain, Panificadora Conquense produces a large range of flours for different applications. To meet these needs, Symaga, based in Villarta de San Juan, Spain, supplied 25 hopper silos of a special height, for total wheat storage capacity of 20,832 tonnes.
The silos included 21 model SCEX0687/21T45EC and four model SCEX0460/09T45EC. Symaga also supplied the catwalks.