KANSAS CITY, MISSOURI, US — With growing demand from the feed, food and fuel industries for vegetable oil and meal, oilseed processors are powering ahead with production expansion and improved efficiency.
High demand and high prices are fueling interest in construction of new processing facilities as well as capacity expansion at existing facilities. Suppliers of oilseed processing equipment are improving their technology to provide more automated and efficient facilities that produce high oil yields and quality meal.
Oilseeds, which include canola, soybeans, sunflower, cottonseed, flaxseed, peanut, palm and coconut, can be processed in a variety of ways, including the use of solvent extraction and mechanical extraction. Processing results in oil for human consumption, biodiesel/fuel production and meal, which is used as high protein livestock and poultry feed.
Processing and extraction processes are designed to produce high-quality oil, with high-extraction yields along with high-value meal. A wide range of equipment is used in the processing, from scalpers, screeners and destoners to dryers, dehullers, cracking mills and flaking mills.
Worldwide, oilseed crushing accounts for 90% of total usage, according to the Organization for Economic Cooperation and Development (OECD)-Food and Agriculture Organization (FAO) Agricultural Outlook. Demand for crush is expected to increase faster than demand for other uses, including direct food consumption of soybeans (including for meat and dairy replacements) as well as direct feeding of soybeans.
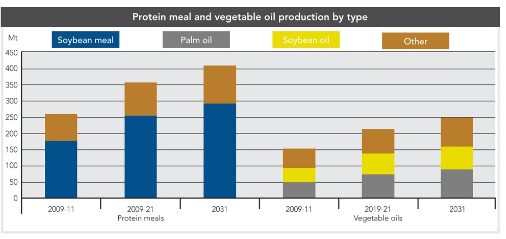
Strong demand for oilseeds and oilseed products pushed prices higher in 2021 and 2022, and OECD-FAO said demand will continue to grow over the next 10 years. Consumption of vegetable oils is expected to reach 249 million tonnes by 2031 with food use accounting for 66% of that total.
Protein meal output is projected to increase 1.1% globally, reaching 410 million tonnes by 2031, OECD-FAO said. It is dominated by soybean meal, which accounts for more than two-thirds of total production. Utilization of protein meal will be constrained by slower growth in global poultry and livestock production, it said.
World Grain interviewed suppliers of oilseed processing equipment about the trends they are seeing in the industry, including equipment requirements and market demands.
Oilseed trends
The feed sector accounts for a large share of the protein use from oilseeds, while human food in the forms of concentrates and isolates still account for a very small share, said Christian Ziemann, head of market segment oilseed processing for Uzwil, Switzerland-based Bühler. In the very long term, there will be a higher percentage going into human food as the need increases for alternative protein sources, especially from soy.
End products will need the highest protein content possible, which will bring changes in the process technology, Ziemann said. However, the feed sector will continue to be the main market for high protein meals.
“This all leads to a further increase in large oilseed crushing plants,” Ziemann said. “It is also becoming apparent that the niche market for organic proteins will develop positively. Here there will be an increase, within a limited scale, in equipment for mechanical extraction, such as pressing by expeller screws.”
While meal production was the focus in the past, efficient and very high oil yield is becoming increasingly important, Ziemann said. This concerns all types of seeds, but especially soy.
Russia’s invasion of Ukraine last February has triggered increased demand for multi-seed crushing equipment, Ziemann said.
“In addition, increased efforts to grow seeds regionally can be seen in some regions in order to be less dependent on imports,” he said. “The serviceability of oilseed crushing plants has also become an increasingly important topic.”
Biofuels production will play an important role now and in the future for the industrial use of vegetable oils, Ziemann said. That is partly driven by subsidies or tax benefits for its use in countries such as the United States and Canada, as well as other parts of the world. There is also a trend toward independence from fossil energy sources and sustainability.
Vegetable oil’s use as a feedstock for biodiesel accounts for 10% to 15% of global usage, OECD-FAO said, and is expected to remain stable over the next 10 years. In the previous decade, usage increased 6.3% as biofuels support policies took effect.
Indonesia, which is the main driver for the increasing use of vegetable oil as a biodiesel feedstock, is expected to use 8.9 million tonnes of oil for fuel production by 2031. Argentina’s export-oriented biodiesel industry is projected to use 1.6 million tonnes of vegetable oil by 2031, equivalent to 56% of domestic vegetable oil consumption, OECD-FAO said.
North America and Asia will have the greatest medium-term need for equipment and technologies, Ziemann said. For example, the demand for biofuels is increasing, especially in North America. The use of vegetable oil for biodiesel, which currently accounts for 15% of global vegetable oil use, is projected to grow in Indonesia, Brazil and the United States.
Population growth and improving living conditions are leading to a higher demand for oil and meat in countries such as China, which is expected to increase its soybean crush by 18 million tonnes in the next 10 years, according to OECD-FAO. That will account for 40% of the world’s additional soybean crush.
On the other hand, due to the limited supply of sunflower seeds and its product from Ukraine and Russia, alternative crushing concepts are necessary to satisfy the demand in Europe and the rest of the world, Ziemann said.
Of all the oilseed varieties, soybeans are taking on an increasingly important role due to higher demand for the high oil and higher protein content end products, Ziemann said. At the same time, the processability is highly standardized, the application is diverse, and the raw material supply is ensured worldwide. Soybean crush is projected to grow by 45 million tonnes in the next 10 years, with soybean oil production reaching 70 million tonnes.
Palm oil production in the last decade has outpaced other vegetable oils, OECD-FAO said, but growth is expected to weaken due to increasing attention to sustainability concerns and the aging of oil palm trees in Indonesia and Malaysia. Those two countries account for more than one-third of the world’s vegetable oil production and more than 80% of global palm oil production.
New technologies
Oilseed crushing plants are characterized by higher protein content in the meal, higher oil yield, lower maintenance, better availability and serviceability, Ziemann said.
Improvements can be seen in the process technologies and the machines used in crushing.
“The process technology improvements are made to gain the highest oil yield and highest protein content in meal, which can be achieved by a very efficient seed cleaning, dehulling and extraction process,” he said. Bühler’s OLCC corrugated roller mill is designed to make operation easier and maintenance simpler. Credit: ©BÜHLER
These new technologies also offer sustainability, energy efficiency and transparency in the process through sensor technology. One of these new products includes Bühler’s OLCC corrugated roller mill, which is designed to make operation easier and maintenance simpler. Features include removable maintenance doors, integrated sampling gates, electronic roller gap adjustment, integrated product bypass and strong permanent magnets. An optional smart human-machine interface allows for full local and remote control over all key functions.
Roller replacement time takes less than two hours per pair. The roller shell is detached from the shaft, so that just the shell is extracted; the complete transmission assembly remains inside the machine. This reduces labor time and handling weight.
Balaguer Rolls, based in Alicante, Spain, is focused on helping customers obtain the best performance in their roller mills and flaking mills. A good profile of the teeth of the rolls is critical for the crushing, said David Balaguer, sales director.
The company recently developed the optical flute test for quality control within the manufacturing facility. It discovered that the test is a great way for monitoring the rolls when they are running.
“We can check the performance of the cracking considering different stages of wear and determine the optimal time for replacing rolls,” Balaguer said. “We also are able to observe the relationships between different variables of the process, such as temperature, moisture, capacity and more. All this technology helps the operators obtain a desirable size distribution.”
Another recent development is the K70 cast that add to the lifetime of the teeth and therefore the roll. This cast leads to a big savings in material and time between roll replacement, Balaguer said, reducing the probability of accidents and eliminating the need for excessive intervention on the equipment.
“The fast evolution of the market and the need of efficiency in oilseed processing is leading to the processors wanting more automation for the overall plant,” he said. “This requires real-time measurement of the product in each step. We are working on higher levels of automation in the maintenance of the flaking rolls, such as in-site roll grinders and roll measurement devices. Also, our fluting machines are designed to be fully automated and faster.”
Future challenges
The oilseed processing industry also is facing some challenges, including the availability of suitable raw materials, Bühler said.
“Oilseed processors are trying to counter this with flexible plant design,” Bühler said. “Multi-seed purpose crushing plants, such as for processing soybeans, rapeseed and sunflower seed, are considered to be able to react flexibly on the market demands.”
Price fluctuations in raw material procurement and the general inflationary effects in plant engineering are important topics. These are countered by long-term contracts and higher standardization in plant engineering. Also, long delivery times must be taken into account, Bühler said.
Additionally, the storage, monitoring and handling of the products is an ongoing issue, but suitable technologies for monitoring and filtration are available.
“The shortage of skilled workers will lead to an increasingly high level of automated equipment with minimal maintenance,” Bühler said. “The desire for high protein and oil yields poses high cost and process-related hurdles. A clear business plan is required to avoid unnecessary investments.”