The tropics are the hottest climate zone on earth. In the countries near the equator, average temperatures range between 25°C and 27°C, and although the efficient and safe handling and storage of grain is a crucial issue everywhere, heavy rains, high ambient temperatures and relative humidity in tropical environments pose significant challenges, such as:
- Processing losses. A large proportion of grain losses occur in storage, but high air temperature and higher humidity of ambient air make the proper drying and storage of material more difficult
- Food safety. About 25% of crops worldwide coming from the field are contaminated with mycotoxins, and additional contamination may occur if grain storage is not optimal. Typical tropical climate conditions mean favorable growing conditions for mycotoxins, mold and pests, making it more difficult to control and minimize the contamination.
- Climate change. With many tropical countries already severely affected by climate change, all processes need to save substantial amounts of water and energy and avoid waste.
Often the level of industrialization in tropical countries is still so low that traditional methods for grain handling remain widely used. But traditional methods have their limits with respect to the above-mentioned challenges. To achieve high yield in an efficient way when operating in a tropical environment — and to ensure food safety — hygienic and energy-efficient industrial processes in grain cleaning, conveying, drying and storage are strongly advised.
Besides that, the harvest volumes of countries around the equator create the need for industrial grain handling solutions. But how do you set up a proper grain handling process?
Grain cleaning
Clean grain handling processes begin with proper cleaning, but in many cases cleaners — if they are used at all — still only remove coarse impurities. To ensure food safety, poisonous impurities and defective grain, along with contaminating spurs, also need to be removed by a comprehensive cleaning process right at the start.
As a positive side effect, removing impurities also means there is less material to be dried and stored. Drying of wet grain down to storage moisture is necessary, and this process step has a huge impact on grain quality.
In tropical countries traditional drying methods, such as sun-drying on the ground — for example, on the street — are still common. But while this is a cheap way to gently dry the crop, it does mean animals can eat the grain. It is also an unhygienic drying process, due to contaminations and pests, and heavy rains can interrupt the drying. The yield is low, the grain is not dried homogeneously, and the storage stability is questionable.
Compared to this, industrial drying processes are much more stable and hygienic. Bühler GmbH’s industrial dryer, for example, dries at high capacity, maximizing the grain’s homogeneity and therefore quality, while at the same time minimizing energy consumption and costs.
To achieve homogeneous drying of the grain and maximum product quality, an optimal airflow within the dryer’s product column is needed — one way to achieve this is Bühler’s patented diagonal arrangement of conical ducts.
A product flow separation step in the drying column also acts as a static mixer, for further improved homogeneity. A perfectly homogeneous drying process not only leads to an optimum product quality but is also highly energy efficient. So, in a controlled way the grain is gently dried to the required storage moisture level.
Grain drying
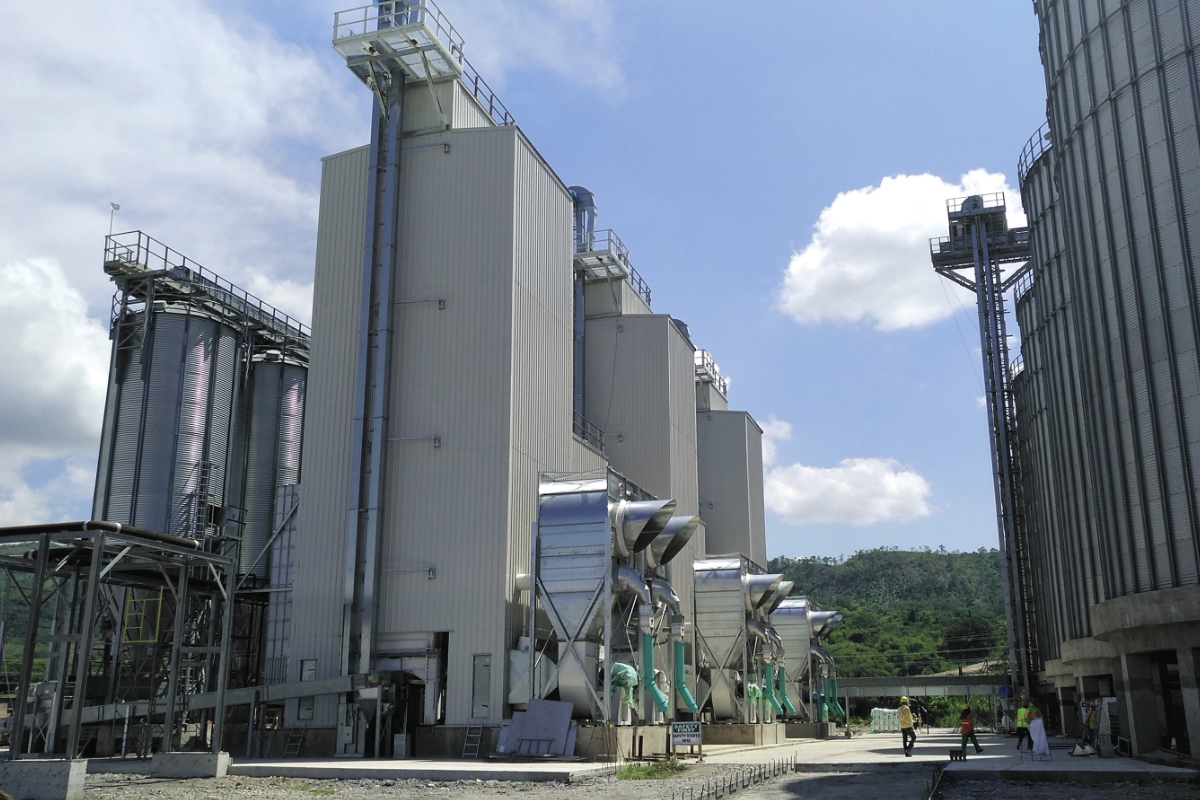
The drying of paddy can be challenging. Even when drying with large capacities, drying speeds are high, and the number of broken grains and energy consumption need to be minimized. Bühler GmbH offers a solution for fast but simultaneously gentle continuous drying of paddy, consisting of a sequence of drying and tempering steps. In the drying steps, the paddy is dried at tailored temperatures depending on the respective moisture levels. In the tempering steps between the drying steps, the moisture can distribute homogeneously within the paddy kernel to minimize the creation of brokens. Compared to conventional processes, this principle saves around 20% of energy at a given higher yield, as the amount of brokens is reduced.
Tropical regions also see many types of biomass used to fire heat sources, and Bühler dryers can be flexibly operated with a huge variety of sources, for example, with steam heat exchangers or indirect biomass furnaces. When appropriate, gas or oil heat sources also may be used.
To protect the environment and to comply with increasingly strict exhaust air regulations, Bühler’s exhaust air handling system minimizes the dust in the exhaust air (< 20 mg/m3 for all grains other than paddy and < 50 mg/m3 for paddy).
Finding skilled operators can be difficult, driving the desire for excellent drying results that can be achieved independently of the operator. Bühler’s DryMate enables the plant manager to achieve optimal drying results and boost the crop’s quality and yield while minimizing energy consumption. DryMate is a digital service comprising an automatic moisture control allowing for automatic drying to the target moisture, as well as dashboards and mobile view for full process transparency and customized tech reports to support the plant’s continuous improvement.
Grain temperature
When storing the material, it is necessary to avoid the creation of hot spots that can cause the degradation of the grain. Keeping the material at lower temperatures means the storage time can be maximized and infestation by pests can be avoided. Given high ambient air temperatures, mere aeration may not be sufficient or may even be harmful due to the warm and humid air entering the silo.
In these cases, the use of one or more coolers is necessary. Here, basically three factors must be managed — temperature, moisture and storage time. Low temperature and low moisture content allow for substantially longer storage times and vice-versa. This is key to success for grain conservation under tropical ambient conditions with high moisture and temperature over most of the day.
Bühler has built up extensive knowledge of the key factors that need to be considered for proper storage, as documented by many successful installations in Southeast Asia.
Energy consumption
A further challenge is energy consumption. Once the target temperature and moisture are achieved, these storage conditions should be maintained in an efficient way by cooling in consecutive cycles to minimize energy use. At the same time, grain losses due to respiration are minimized and insect exposure is significantly reduced.
It is Bühler’s aim to provide solutions by 2025 that allow for 50% reduction in each of the following areas: water consumption, energy consumption and waste in the value chain.
To achieve this target, Bühler is developing new digital service innovations such as Bühler Insights silo monitoring, which allows ambient and grain conditions (temperature and moisture) to be monitored. The user can set alarm levels based on critical and warning temperatures — all layers in a silo can be easily monitored and the aeration and cooling precisely adjusted, saving energy and optimizing grain quality.
The user receives notifications once a deviation of the defined parameters appears, enabling instant action and avoiding discoloration and grain losses as a result of hotspots. A comprehensive contemporary industrial solution is therefore able to tackle the biggest grain storage challenges in a tropical environment: Operational costs are minimized by energy-saving solutions and yields are maximized compared to traditional grain handling methods.
Using Bühler’s industrial grain handling solutions, process losses are minimized as proper cleaning preserves the “good material,” homogeneous drying to the exact target moisture maximizes the yield, and carefully controlled storage minimizes losses in the silos. And crucially, food safety is ensured by comprehensive cleaning, exact and hygienic drying, and proper storage to keep the grain in a healthy and safe condition.
Volker Josel and Saioa Villodas are grain storage product managers at Bühler. They may be reached at volker.josel@buhlergroup.com or saioa.villodas@buhlergroup.com.