UZWIL, SWITZERLAND — In today’s dynamic landscape of animal feed production, several key challenges and trends are reshaping the industry. With rising energy costs, increased pressure for sustainability, and a growing emphasis on quality and efficiency, feed manufacturers are looking for innovative solutions to meet these demands. Digitalization and automation have emerged as powerful tools, paving the way for a future where “smart” feed mills could operate autonomously. One significant step toward this vision is the control of pellet moisture, a feature made possible by Bühler’s PelletingPro.
The animal feed production industry operates in a competitive market characterized by thin profit margins. Raw material prices, including grains, extraction meals, and oil cakes, fluctuated strongly in recent years and this trend likely will continue. Simultaneously, there is a shift toward utilizing locally available products and byproducts, each with its own unique pelleting characteristics. Another challenge is the availability of well-educated and experienced personnel, which is becoming scarcer.
In this ever-evolving landscape, feed manufacturers face the following critical challenges:
Efficiency: With the demand for animal protein continually growing, the need for highly efficient production plants has never been greater.
Pellet quality: Ensuring consistent and high-quality pellets is paramount to meet the nutritional needs of animals.
Workforce: A less experienced workforce combined with high personnel turnover poses operational challenges.
Raw material quality: Fluctuating raw material quality adds complexity to the production process.
Sustainability: The imperative to reduce carbon emissions and enhance the sustainability of feed production is driving the industry.
Digitalization and automation: a necessity
To address these challenges, digitalization, automation and data science are becoming indispensable tools for feed manufacturers. These tools may be used for increased process transparency by continuously monitoring and evaluating material and process data. These insights allow data-driven decision-making, leading to an improved performance by increasing overall efficiency and therefore competitiveness.
The greatest challenge in the industry today is developing the logic of the semantic data and process model, describing the dependencies of input variables, and selecting appropriate datasets to train and test the algorithm. Since feed ingredients are agricultural commodities, they are exposed to many influencing factors such as climate or transport and storage conditions, increasing the challenge.
Pellet moisture control
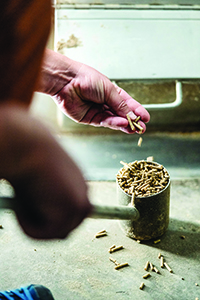
One of the most significant steps toward a “smart” feed mill is the control of pellet moisture. Pellet moisture plays a pivotal role in feed production, as excess moisture can lead to spoilage and product returns, resulting in substantial losses for manufacturers. To mitigate this risk, feed producers often opt to make their feed drier than ideal, sacrificing product volume.
Controlling moisture is a formidable challenge due to numerous influencing factors, including raw material characteristics, storage conditions, and seasonal variations. Recent disruptions in the supply chain have forced factories to adapt production formulas rapidly, making moisture control more challenging than ever.
Although still bound by the rules of physics and therefore not completely arbitrarily applicable, a pellet moisture control loop can already be implemented today. Experience shows that the use of such a system increases process stability. This leads to a whole series of advantages, such as:
Independent of operator: The stabilized process runs smoothly and reliably. Even an inexperienced operator can thus supervise several pellet lines, making pelleting less dependent of professional expertise.
Increased production: A stable running pellet mill will have less unplanned downtime and thus be able to produce up to 20% more feed per year and pelleting line.
Reduced energy requirements: Due to the lubricating effect of the additionally added water, the pellet mill will require up to 20% less energy per tonne of feed produced. In this context, it is important to note that it has been proven that this has no negative effect on the PDI.
Increased yield: Precise dosing of the water content in the finished pellet leads to a yield increase of up to 1%, enhancing plant profitability.
However, an automated system is only as good as in its weakest moments. In other words, it must itself recognize critical situations such as sensor failure and initiate appropriate measures. Otherwise, the process or the entire plant can be transferred to a critical state.
PelletingPro advantage
Bühler’s PelletingPro offers precise control of pellet moisture. With PelletingPro a final pellet moisture deviation of just +/- 0.5 percentage points from a target value set by the operator is achievable. This is accomplished through the targeted collection and evaluation of process data, which is fed into a physical model of the process. Self-checking of input and output values, described above, ensures safe and reliable operation.
PelletingPro is used worldwide, covering different production volumes of ruminant, swine and poultry feed. One Central European customer who uses PelletingPro since 2021 could stabilize the variation of his final pellet moisture below +/- 0.5 percentage points. Having a total production of more than 200,000 tonnes per annum on the lines running with PelletingPro, his return on investment was less than a year.
Sustainable solution
As sustainability gains prominence in the feed industry, PelletingPro contributes to reducing carbon emissions. In light of the Intergovernmental Panel on Climate Change’s (IPCC) warning to limit global warming to 1.5°C above pre-industrial levels, having an energy-saving process contributes greatly to this goal. For a typical pelleting line with 100,000 tonnes of annual throughput, PelletingPro can save up to 2,000 tonnes of CO2 equivalent per year. This equals the annual carbon drawdown capacity of 100,000 trees.
In a rapidly changing and highly competitive feed industry, an automized process optimization becomes state of the art. By addressing challenges related to moisture control, efficiency and sustainability, PelletingPro helps feed manufacturers optimize their operations, reduce costs, and contribute to a more sustainable future.
Mark Werthmann is a process engineer with Bühler. He may be reached at [email protected].